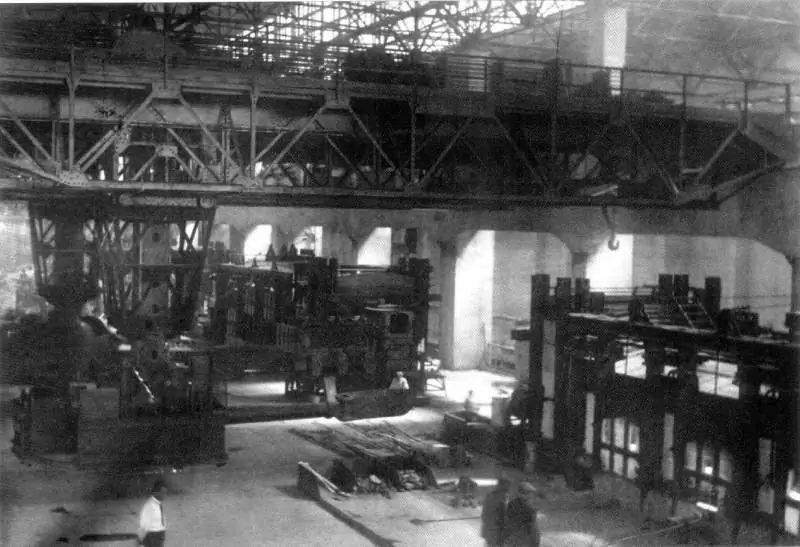
Strateginis šaltinis
Karo sąlygomis sunku pervertinti aukštos kokybės plieno gamybą kariniam ir pramoniniam kompleksui. Tai yra vienas iš svarbiausių veiksnių, lemiančių armijų sėkmę mūšio lauke.
Kaip žinote, „Krupp“metalurgai vieni pirmųjų išmoko gaminti aukštos kokybės ginklų plieną.
Pabaigoje vokiečiai priėmė Tomo gamybos procesą. Šis plieno lydymo metodas leido iš rūdos pašalinti fosforo priemaišas, kurios automatiškai pagerino gaminio kokybę. Aukštos kokybės šarvai ir ginklų plienas Pirmojo pasaulinio karo metu dažnai užtikrino vokiečių pranašumą mūšio lauke.
Norint organizuoti tokią gamybą, reikėjo naujų ugniai atsparių medžiagų, išklotų vidinius krosnių paviršius. Vokiečiai savo laikui naudojo naujausius ugniai atsparius magnezitus, atlaikančius daugiau nei 2000 laipsnių temperatūrą. Tokios didesnio atsparumo ugniai medžiagos yra pagamintos iš magnio oksidų su nedideliais aliuminio oksidų priedais.
XX amžiaus pradžioje šalys, turinčios masinės ugniai atsparių ugniai atsparių medžiagų gamybos technologijas, galėjo sau leisti gaminti aukštos kokybės šarvus ir ginklų vamzdžius. Tai galima palyginti su strateginiu pranašumu.
Mažesnės atsparumo ugniai atžvilgiu buvo vadinamosios labai ugniai atsparios medžiagos, kurios atlaiko temperatūrą nuo 1750 iki 1950 laipsnių. Tai yra dolomito ir didelio aliuminio oksido ugniai atsparios medžiagos. Šamotinės, pusiau rūgštinės, kvarco ir dinos ugniai atsparios medžiagos gali atlaikyti 1610-1750 laipsnių temperatūrą.
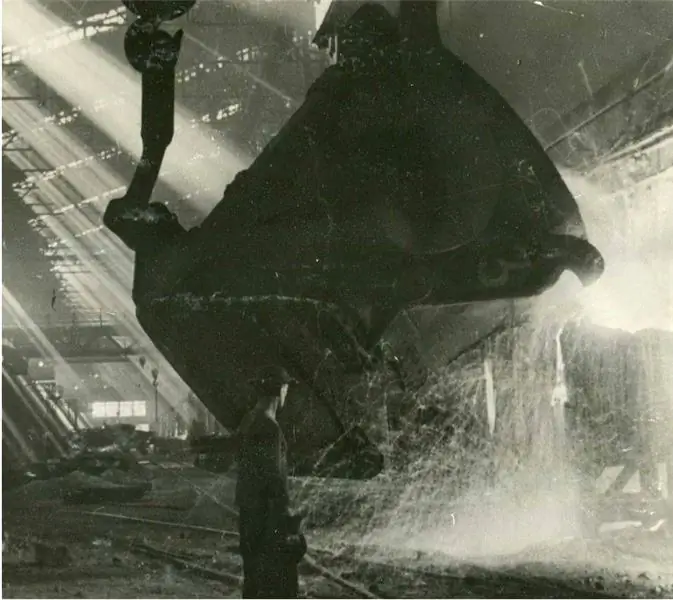
Beje, magnezito ugniai atsparių medžiagų gamybos technologijos ir vietos pirmą kartą pasirodė Rusijoje dar 1900 m.
Ugniai atspari plyta „Satka“1905 metais buvo apdovanota aukso medaliu Pasaulio pramonės parodoje Lježe. Jis buvo pagamintas netoli Čeliabinsko Satkos mieste, kur buvo unikalus magnezito telkinys.
Periklazės mineralas, iš kurio gamykloje buvo pagaminti ugniai atsparūs produktai, buvo aukštos kokybės ir nereikalavo papildomo praturtinimo. Dėl to ugniai atsparus magnezitas iš Satkos buvo pranašesnis už analogus iš Graikijos ir Austrijos.
Skirtumo mažinimas
Nepaisant gana aukštos kokybės magnezito plytų iš Satkos, iki 30-ųjų, pagrindiniai sovietinių metalurgų ugniai atsparūs elementai buvo dinas iš molio. Natūralu, kad aukšta temperatūra ginklų plieno lydymui nepasiteisino-atviro židinio krosnių vidinis pamušalas subyrėjo ir reikalavo nepaprasto remonto.
„Satka“plytų nepakako, o po revoliucijos pagrindinės gamybos technologijos buvo prarastos.
Tuo pat metu europiečiai žengė į priekį - pavyzdžiui, austrų „Radex“magnezitas išsiskyrė puikiu atsparumu ugniai.
Sovietų Sąjunga įsigijo šią medžiagą. Tačiau neįmanoma gauti analogo be gamybos paslapties. Šią problemą ėmėsi Maskvos valstybinio technikos universiteto absolventas. N. E. Baumanas Aleksejus Petrovičius Panarinas. „Magnet“gamykloje (buvęs „Satka“kombinatas) 1933 m. Vadovavo Centrinei augalų laboratorijai. Ir po penkerių metų jis pradėjo masinę periklazės-chromito arba chromomagnezito ugniai atsparių ugniai atsparių krosnių gamybą.
„Zlatoust“metalurgijos gamykloje ir Maskvos plaktuku bei pjautuvu Panarino ugniai atsparios medžiagos pakeitė pasenusias dinas.
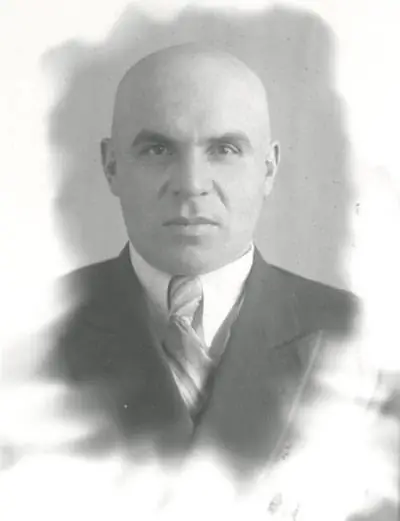
Technologija, kuri keletą metų buvo kuriama „Magnezit“laboratorijoje, susideda iš ypatingos sudėties ir dalelių dydžio.
Anksčiau gamykla gamino įprastas chromo-magnezito plytas, sudarytas iš magnezito ir chromo geležies rūdos santykiu 50/50. Panarino grupės atskleista paslaptis buvo tokia:
„Jei į paprastą magnezito krūvį pridedama chromito rūdos šiurkščiuose granulometriniuose grūduose, kurių mažiausias frakcijų kiekis yra mažesnis nei 0,5 mm, tai net ir pridedant 10% tokios rūdos, plytų šiluminis stabilumas smarkiai padidėja.
Didėjant šiurkščiavilnių granulometrijos chromito rūdos kiekiui, plytų stabilumas auga ir pasiekia maksimumą esant tam tikram komponentų santykiui “.
Chromitas naujam ugniai atspariam medžiagui buvo paimtas Saranovskoje kasykloje, o periklazė buvo toliau kasama Satkoje.
Palyginimui, įprasta „priešrevoliucinė“magnezito plyta atlaikė 5-6 kartus žemesnę temperatūrą nei Panarino naujovė.
Kirovogrado vario lydymo gamykloje chromo-magnezito ugniai atsparus atspindintis krosnies stogas 151 dieną atlaikė iki 1550 laipsnių temperatūrą. Anksčiau ugniai atsparias medžiagas tokiose krosnyse reikėdavo keisti kas 20-30 dienų.
Iki 1941 m. Buvo įvaldyta didelio masto ugniai atsparių medžiagų gamyba, o tai leido medžiagas naudoti didelėse plieno gamybos krosnyse iki 1800 laipsnių temperatūros. Prie to svariai prisidėjo „Magnezit“technikos direktorius Aleksandras Frenkelis, sukūręs naują ugniai atsparios medžiagos tvirtinimo prie krosnių stogų metodą.
Ugniai atsparūs pergalei
1941 m. Pabaigoje Magnitkos metalurgai įvykdė anksčiau neįsivaizduojamą dalyką-pirmą kartą istorijoje jie įvaldė šarvuoto plieno lydymą tankams T-34 pagrindinėse sunkiose atviro židinio krosnyse.
Pagrindinis ugniai atsparių medžiagų tiekėjas tokiam svarbiam procesui buvo Satka „Magnezit“. Nereikia kalbėti apie karo laikų sunkumus, kai trečdalis gamyklos darbuotojų buvo iškviesti į frontą, o valstybė pareikalavo, kad planas būtų perpildytas. Nepaisant to, gamykla atliko savo darbą, o Panarinas 1943 m
„Užvaldyti labai ugniai atsparių gaminių gamybą iš vietinių juodosios metalurgijos žaliavų“
buvo apdovanota Stalino premija.
1944 metais šis metalurgas-tyrėjas sukurs aukštos kokybės magnezito miltelių „Extra“gamybos technologiją. Iš šio pusgaminio buvo gaminamas presuotas ugniai atsparus produktas, naudojamas ypač svarbioje šarvuoto plieno gamyboje elektrinėse krosnyse. Tokių ugniai atsparių temperatūrų riba pasiekė 2000 laipsnių.
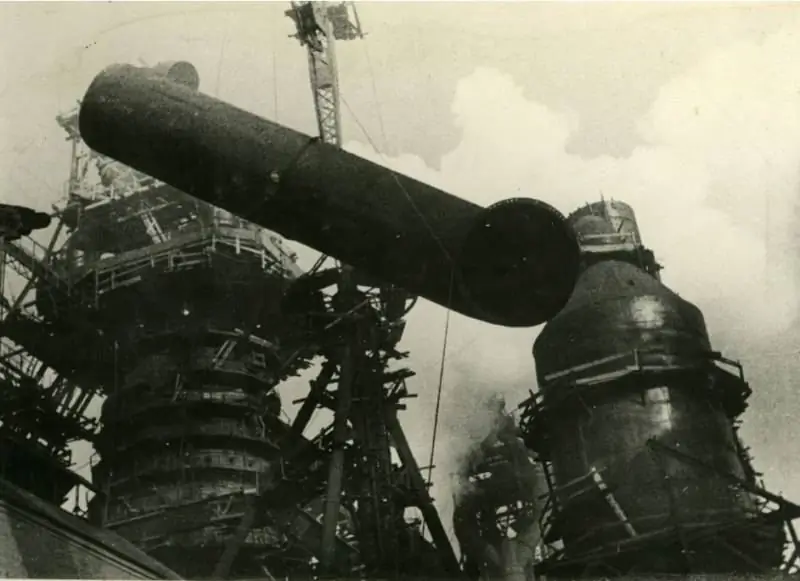
Tačiau nereikėtų manyti, kad apskritai sėkmingos „Magnezit“gamyklos pavyzdys buvo taikomas visai Sovietų Sąjungos ugniai atspariai pramonei.
Ypač sunki situacija susiklostė Urale, kur 1941-1942 m. Buvo evakuota praktiškai visa šalies tankų pastatas.
Magnitogorsko ir Novotagilsko metalurgijos gamyklos buvo perorientuotos į šarvų gamybą, tiekdamos gaminius į Sverdlovsko Uralmash, Čeliabinsko „Tankograd“ir Nižnij Tagil tankų gamyklą Nr. 183. Tuo pačiu metu metalurgijos gamyklos turėjo savo ugniai atsparių medžiagų gamybą iš vietinių žaliavų.
Pavyzdžiui, Magnitkoje dinas-chamotte gamykla per metus pagamino 65-70 tūkst. To nepakako net jų pačių poreikiams, jau nekalbant apie tiekimą kitoms įmonėms.
Pirmieji sunkumai kilo, kai cisternų gamyklos pradėjo kurti savo šildymo ir termines krosnis. Uralo metalurgija jau beveik neturėjo pakankamai ugniai atsparių medžiagų, tada tankų gamyklų korpuso gamybai reikėjo aukštos kokybės medžiagų krosnims pamušti.
Čia nebuvo kalbama apie jokius chromomagnezito ugniai atsparius elementus - šios medžiagos trūko ir netgi buvo eksportuojama mainais už „American Lend -Lease“. Bent jau apie tai kalbama daugelyje šaltinių. Uralo istorikai rašo, kad brangus Panarino chromomagnezitas gali išvykti į užsienį mainais į negausius geležies lydinius už tankų šarvus. Tačiau tiesioginių to įrodymų kol kas nėra.
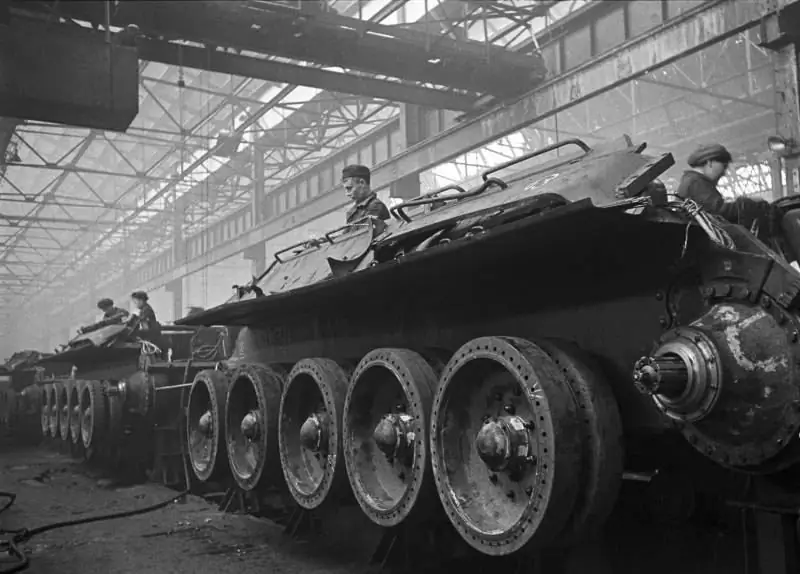
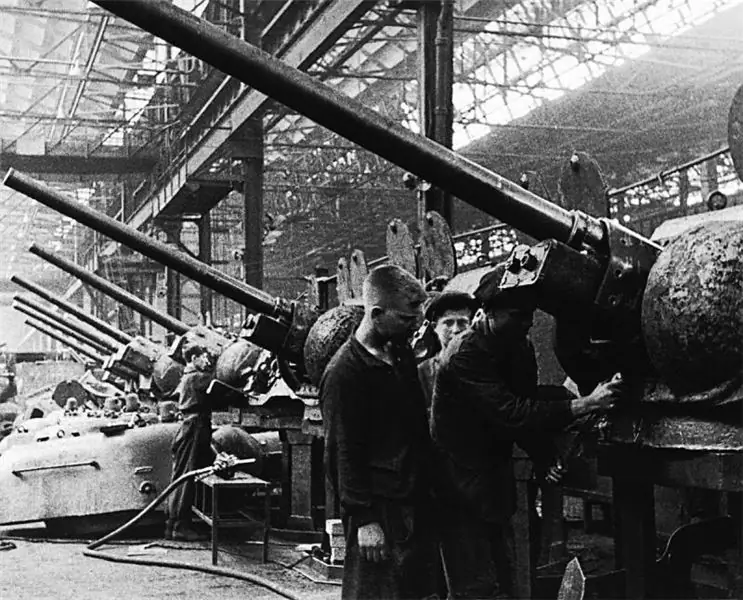
Cisternų gamyklos daugiausia rėmėsi Dinas ugniai atsparia medžiaga, pagaminta Pervouralsko gamykloje. Bet, pirma, jis buvo pagamintas tik 12 tūkstančių tonų per mėnesį, ir, antra, metalurgai užėmė liūto dalį.
Gamybos plėtra Pervouralsko gamykloje vyko labai lėtai. Ir iki 1942 metų vidurio atsirado tik 4 naujos krosnys. Kiti nebuvo pasirengę arba paprastai egzistavo tik projektuose.
Ugniai atsparios cisternų gamyklų krosnių krosnys dažnai buvo nekokybiškos, ne visos ir netinkamu laiku. Tik „Uralmash“krosnių remontui 1942 m. Ketvirtąjį ketvirtį reikėjo 1035 tonų ugniai atsparių plytų ir tik apie 827 tonas.
1943 m. „Uralmash“atviro židinio parduotuvė apskritai beveik sustojo, nes trūko remontui atsparių ugniai atsparių medžiagų.
Viso karo metu tiekiamų ugniai atsparių medžiagų kokybė paliko daug norimų rezultatų. Jei normaliomis sąlygomis atviro židinio krosnies dinas galėjo atlaikyti 400 įkaitimų, tai karo metu jis neviršijo 135 karščių. Ir iki 1943 metų kovo šis parametras nukrito iki 30-40 karščių.
Ši situacija aiškiai parodo, kaip vieno išteklio (šiuo atveju ugniai atsparių) trūkumas gali rimtai sulėtinti visos gynybos pramonės darbą. Kaip savo darbuose rašo istorijos mokslų kandidatas Nikita Melnikovas, 1943 m. Kovo mėn. Trys Uralmašo krosnys su atviru židiniu vis tiek sustojo ir atliko visą remonto darbų ciklą. Tam prireikė 2346 tonų dinų, 580 tonų šamoto ir 86 tonų negausus magnezito.
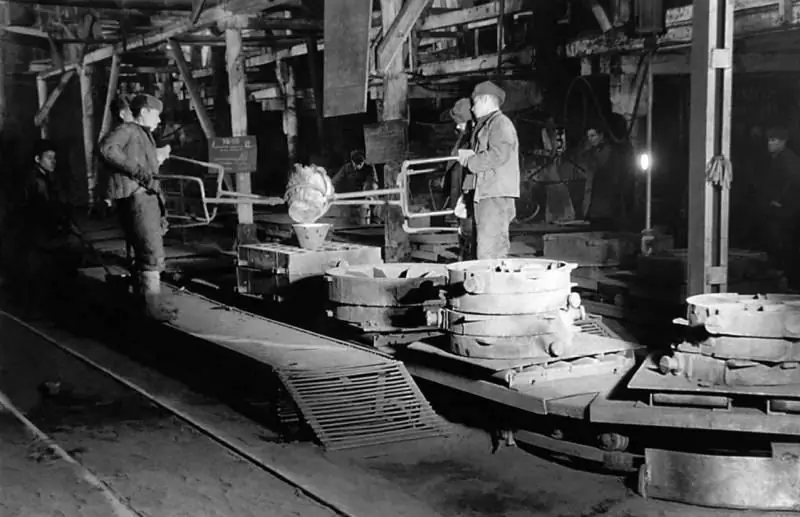
Iki 1942 m. Vidurio cisternų gamykloje Nr. 183 situacija vystėsi panašiai - plieno gamyba atsiliko nuo mechaninio surinkimo. Ir mes turėjome „importuoti“T-34 korpusus iš Uralmash.
Viena iš priežasčių buvo ugniai atsparių medžiagų trūkumas remontuojant atviro židinio krosnis, kurios 1942 m. Pavasarį dirbo maksimaliai. Dėl to rudenį veikė tik 2 iš 6 atviro židinio krosnių, lydymo apimtys buvo atkurtos tik 1943 m.
Padėtis su ugniai atspariomis sovietų gynybos komplekso struktūromis Didžiojo Tėvynės karo metu aiškiai iliustruoja padėties šalies gale sudėtingumą.
Lėtinis, apskritai, ne pačių aukščiausių technologijų produktų trūkumas tiesiogiai paveikė šarvuotų transporto priemonių gamybos tempą.